My senses were on overload as I walked through the side door leading into a bay area with two lifts. On one of the lifts was a teal-colored Jeepster. On the other, a stunning blue Cherokee Chief. And resting near the rear entryway, a completely stripped-down white Cherokee Chief awaited its resurrected life as a modern classic. It was as if I had entered a modern-day Dr. Frankenstein laboratory, only this time it wasn’t a person being resurrected. It was a slew of old school Jeeps whose previous life had been completely worn and had entered a transitionary phase en route to becoming much improved. It was akin to Jeep Life 2.0. The doctor? Daniel van Doveren and his crew at Jeep Heritage.
I’ve had an affinity for the old school allure of Jeep-branded vehicles since I was a kid, and I’ve always been impressed by the work of artisans – that’s how I see them – who give vehicles a second life that maintains the vehicle’s classic beauty but integrates modern technology under their skin. That’s exactly what Texas-based Jeep Heritage does.
When I first met Daniel, proprietor of Jeep Heritage who hails from Belgium, I was thrilled to meet a fellow enthusiast who has taken his multitude of skillsets and passion for the brand and turned them into something he does for a living. You can’t help but notice the time and attention to detail that goes into each resurrected vehicle, literally piece by piece, many of which includes platforms such as Cherokee Chiefs, Grand Wagoneers, and J-10 Honchos but can include virtually any vintage Jeep branded vehicle.
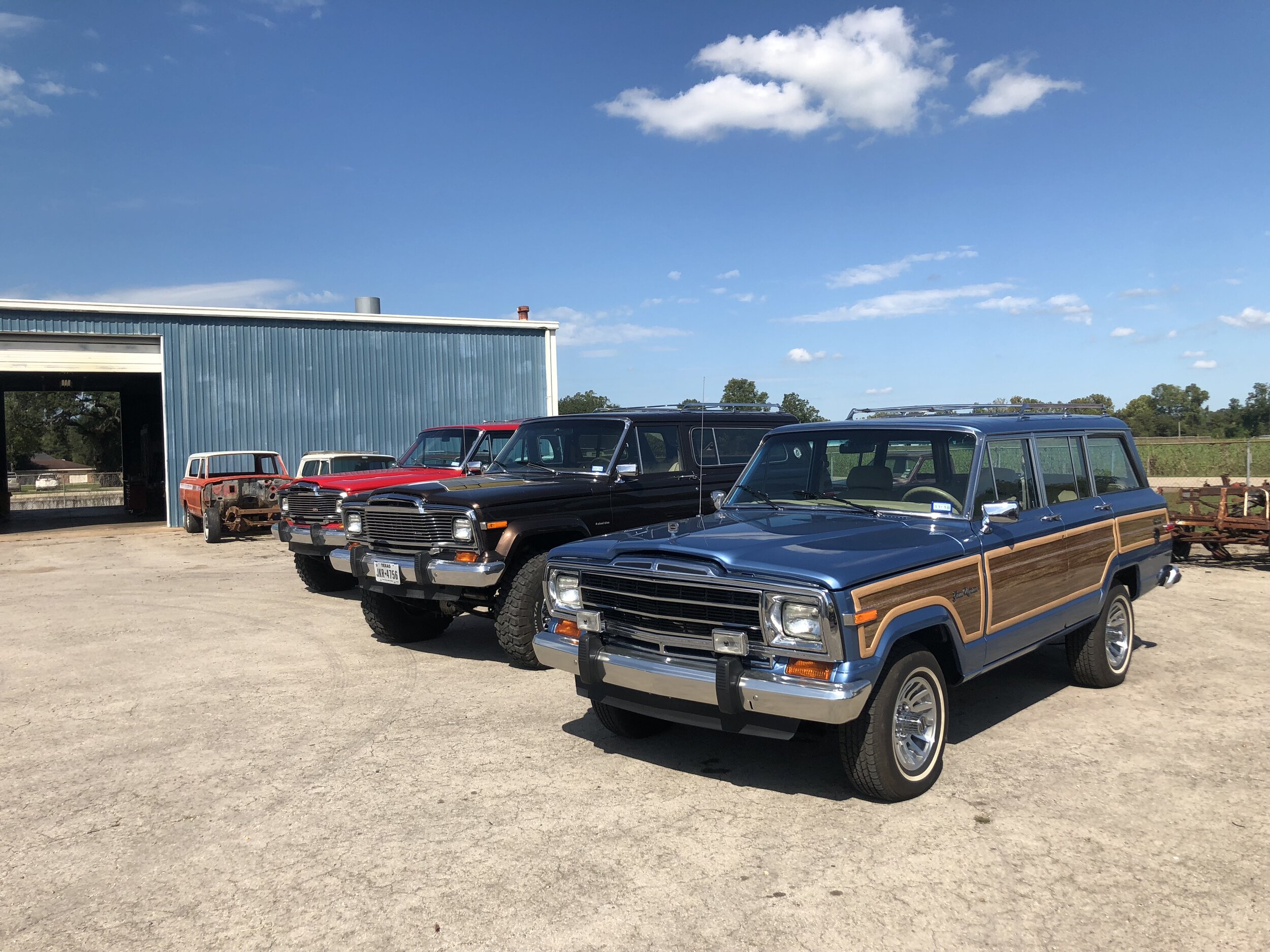


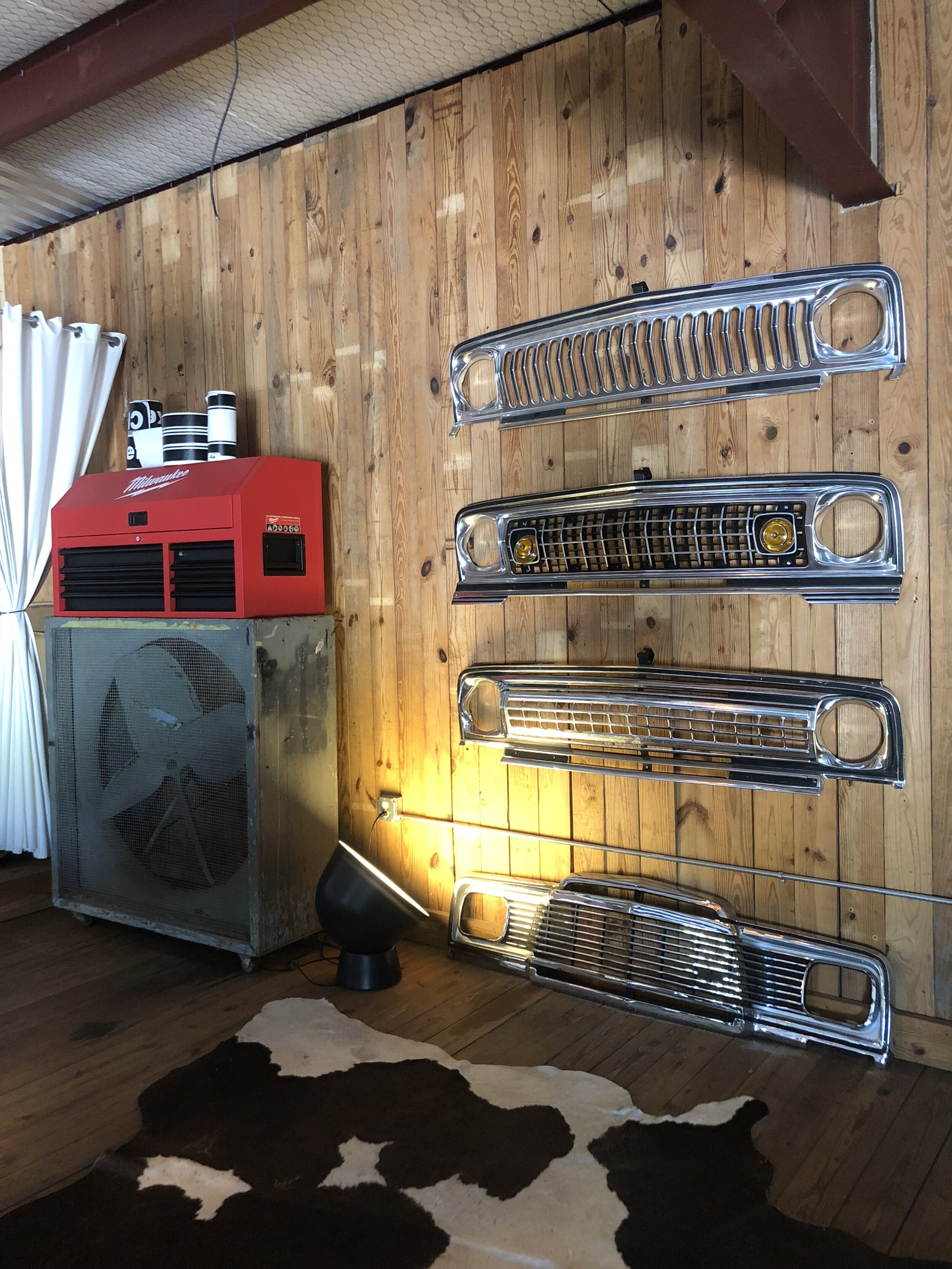
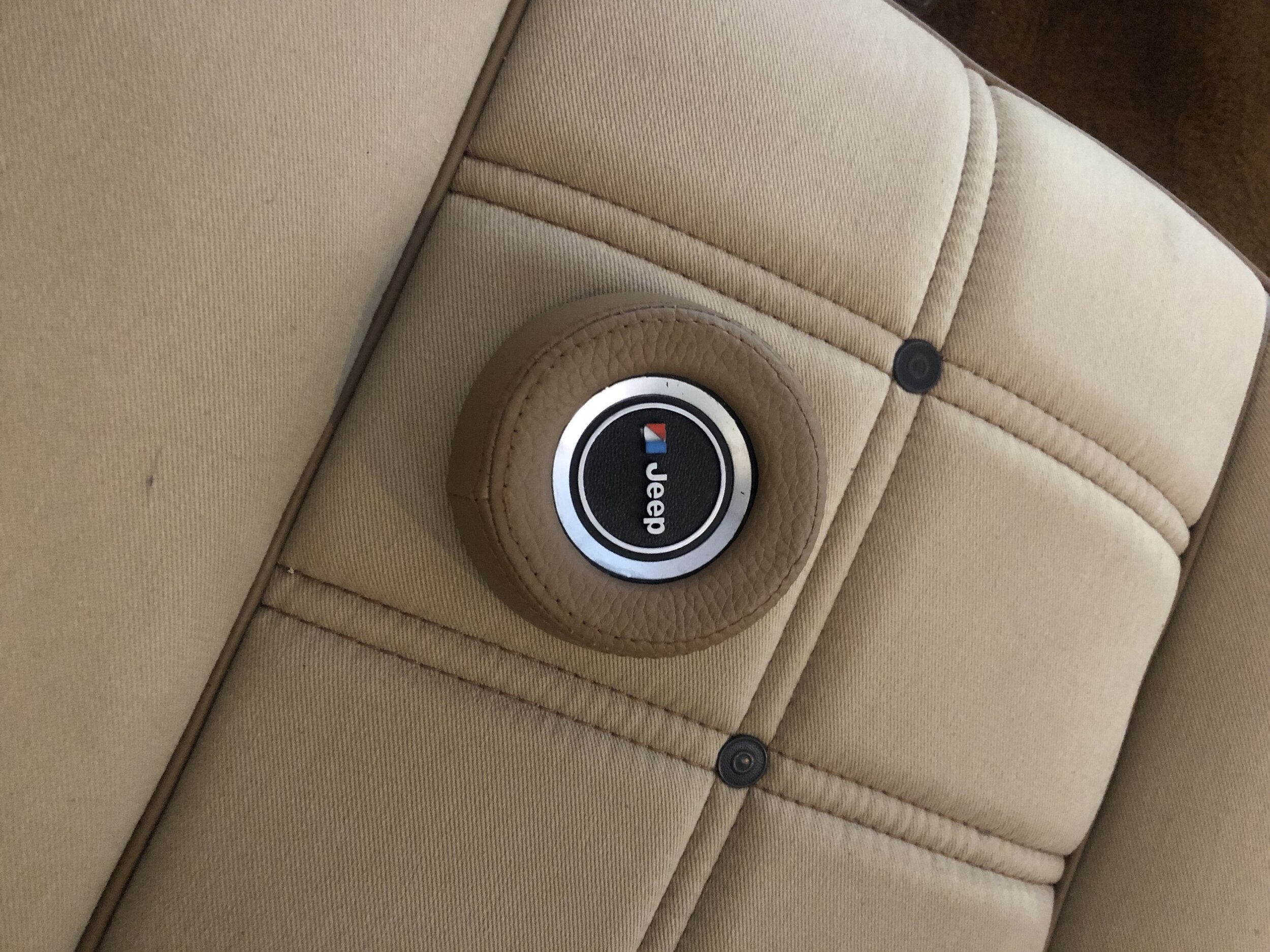
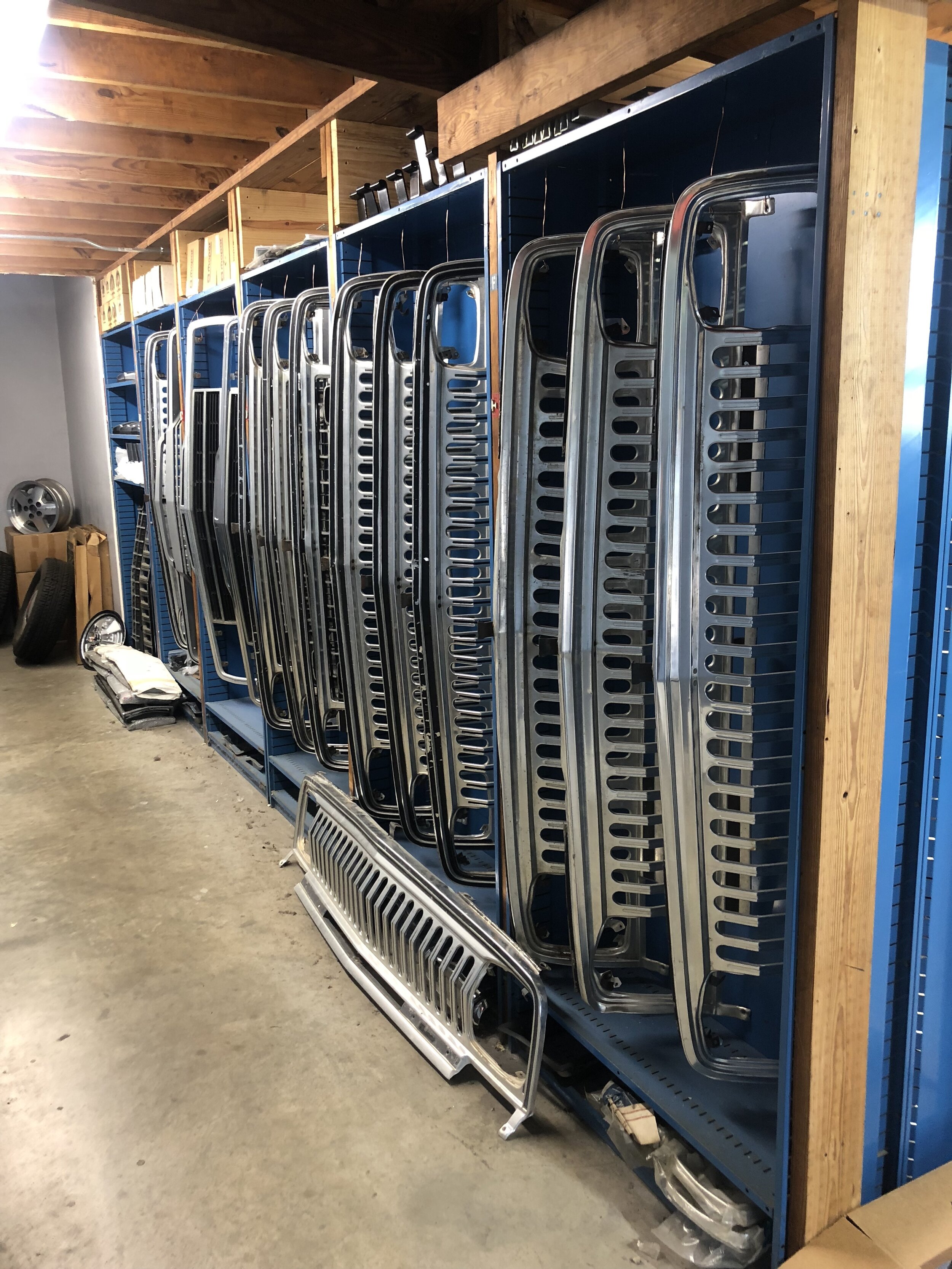
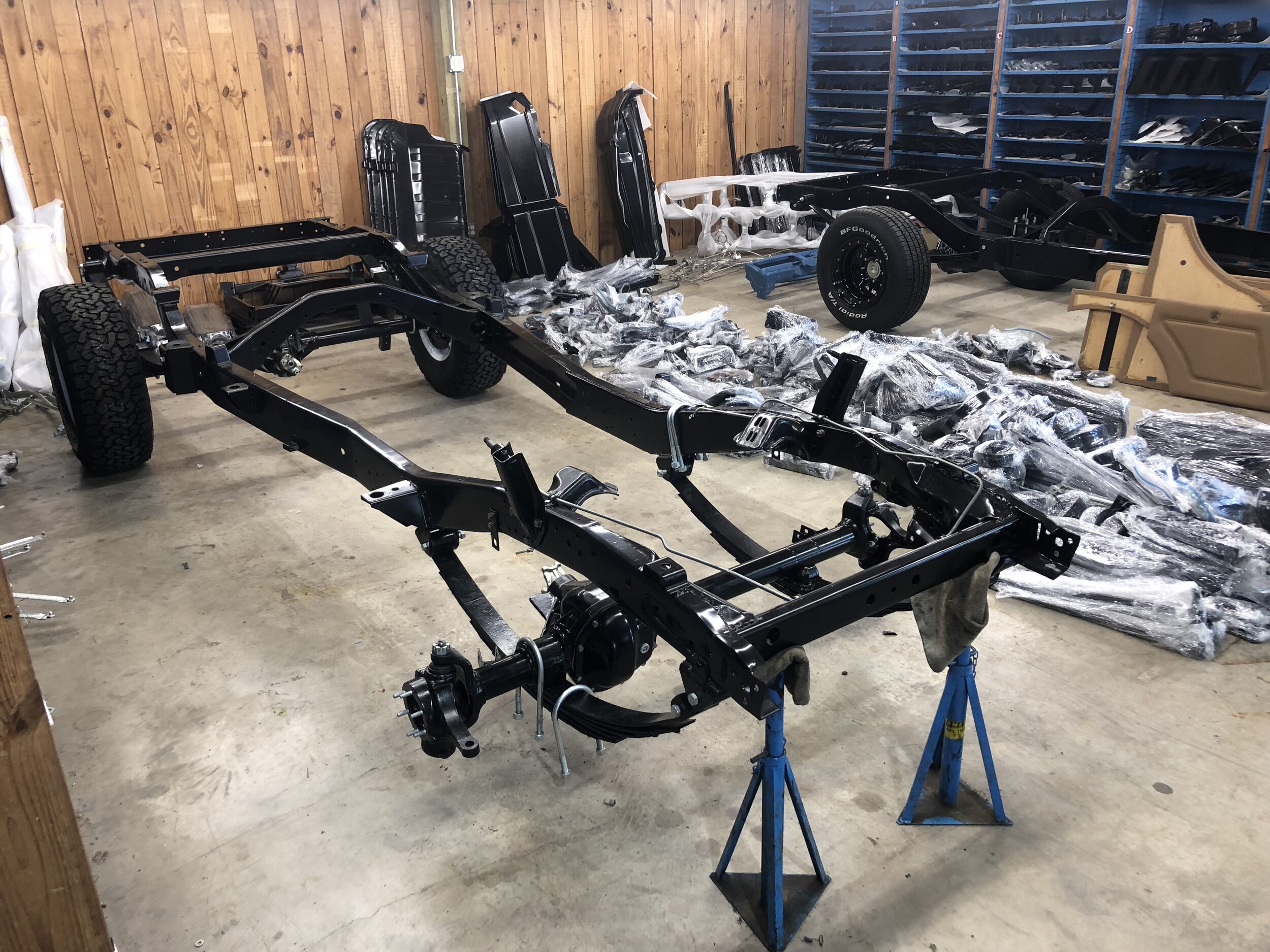
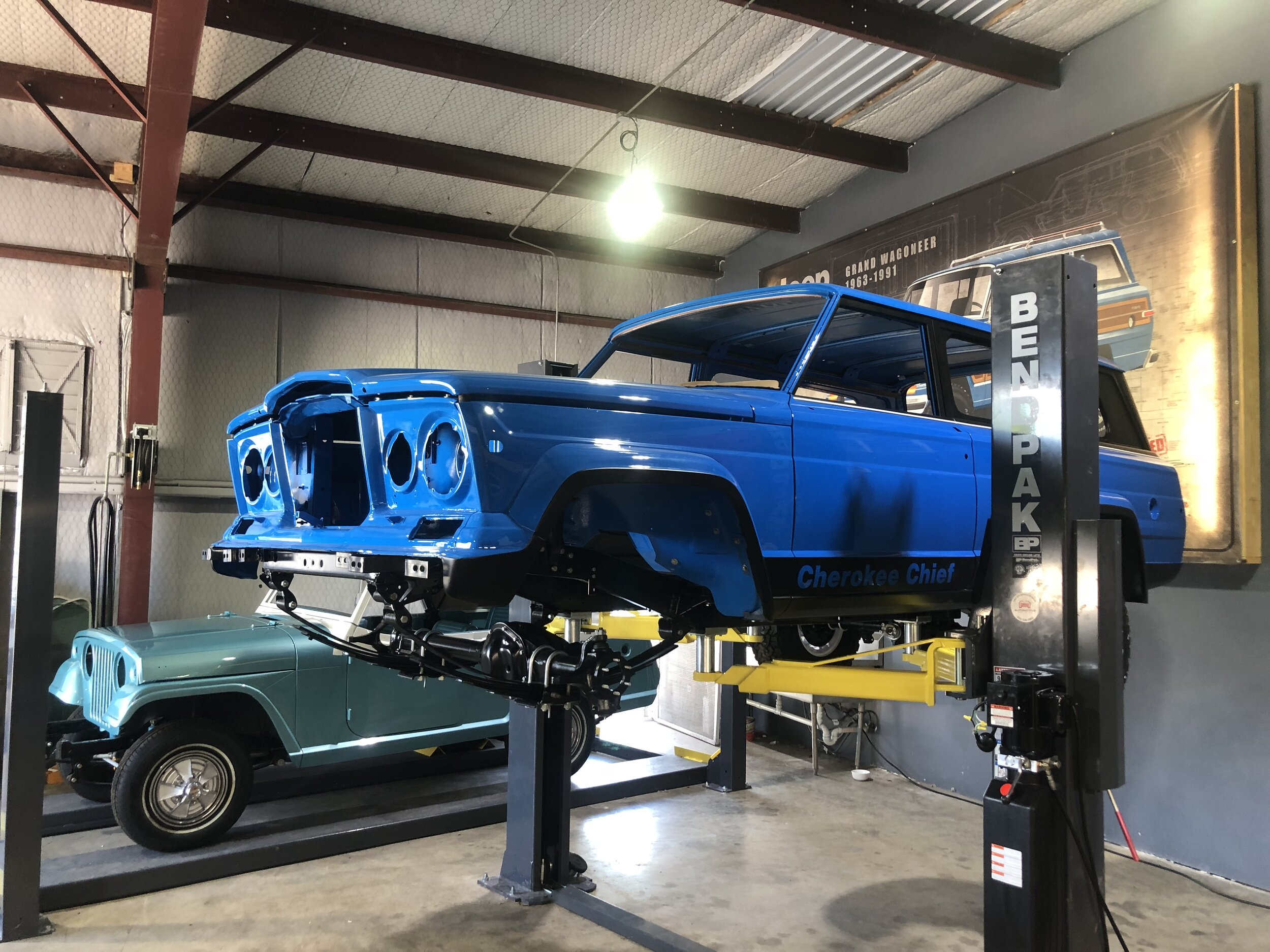
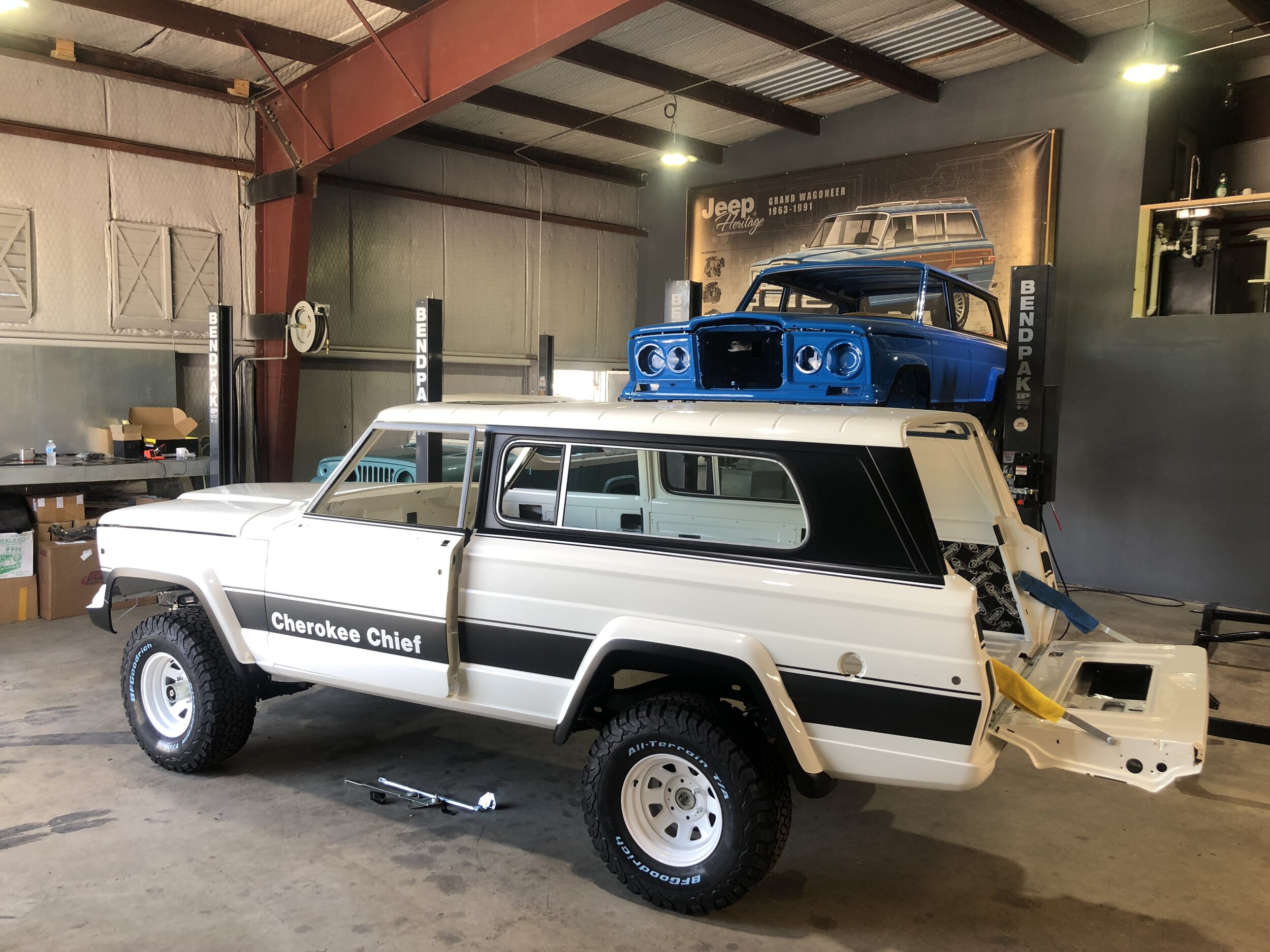
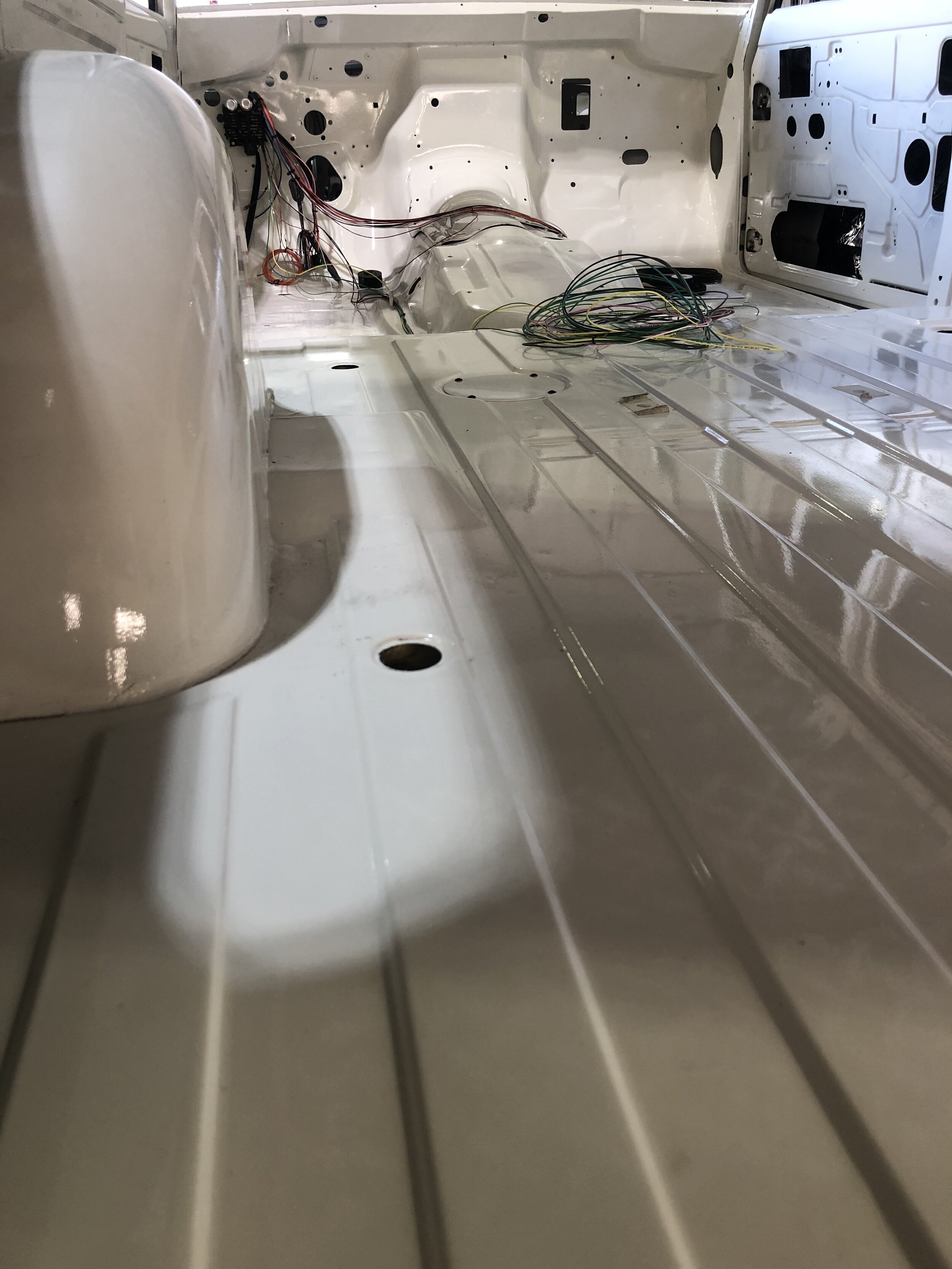
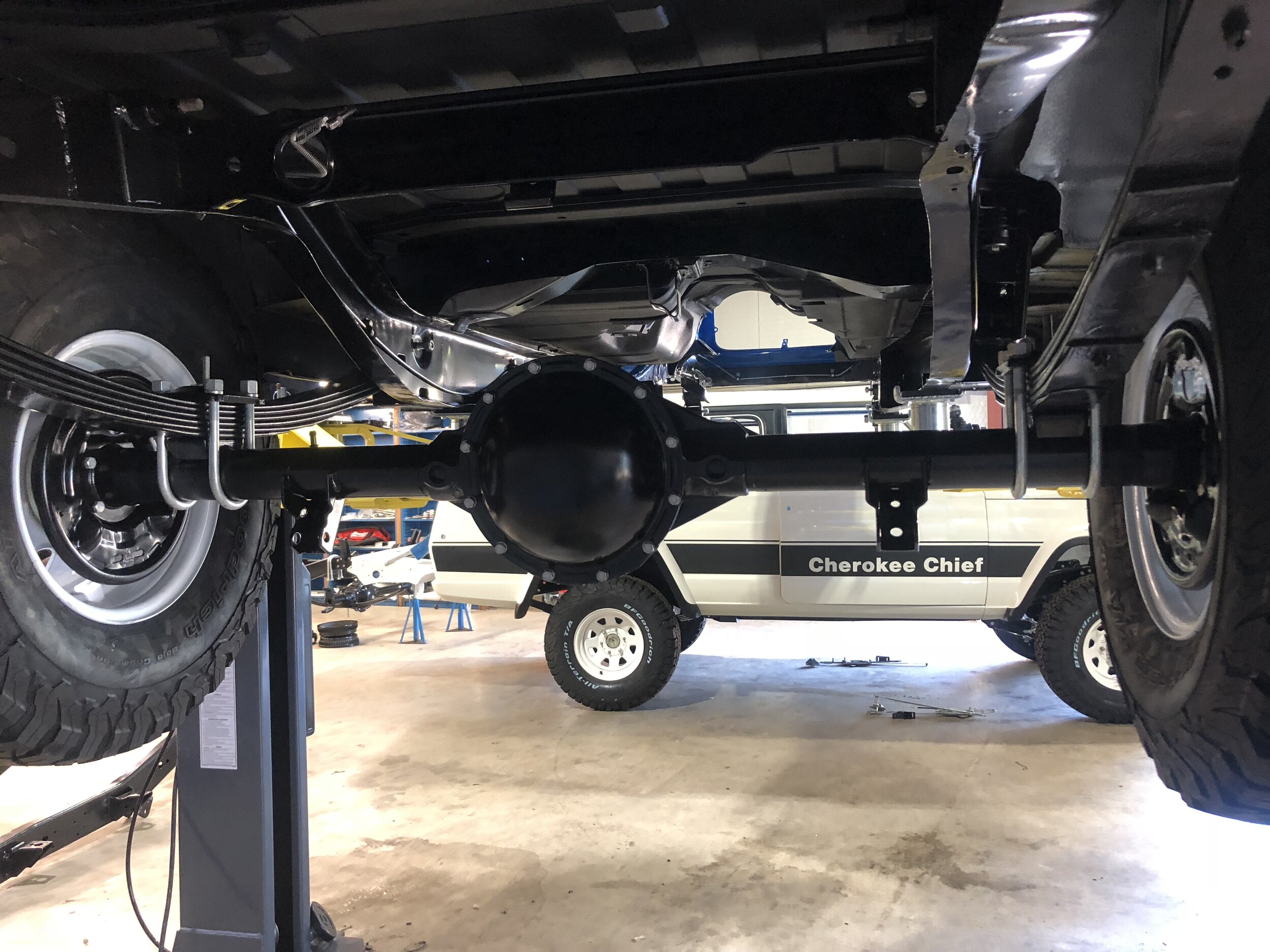
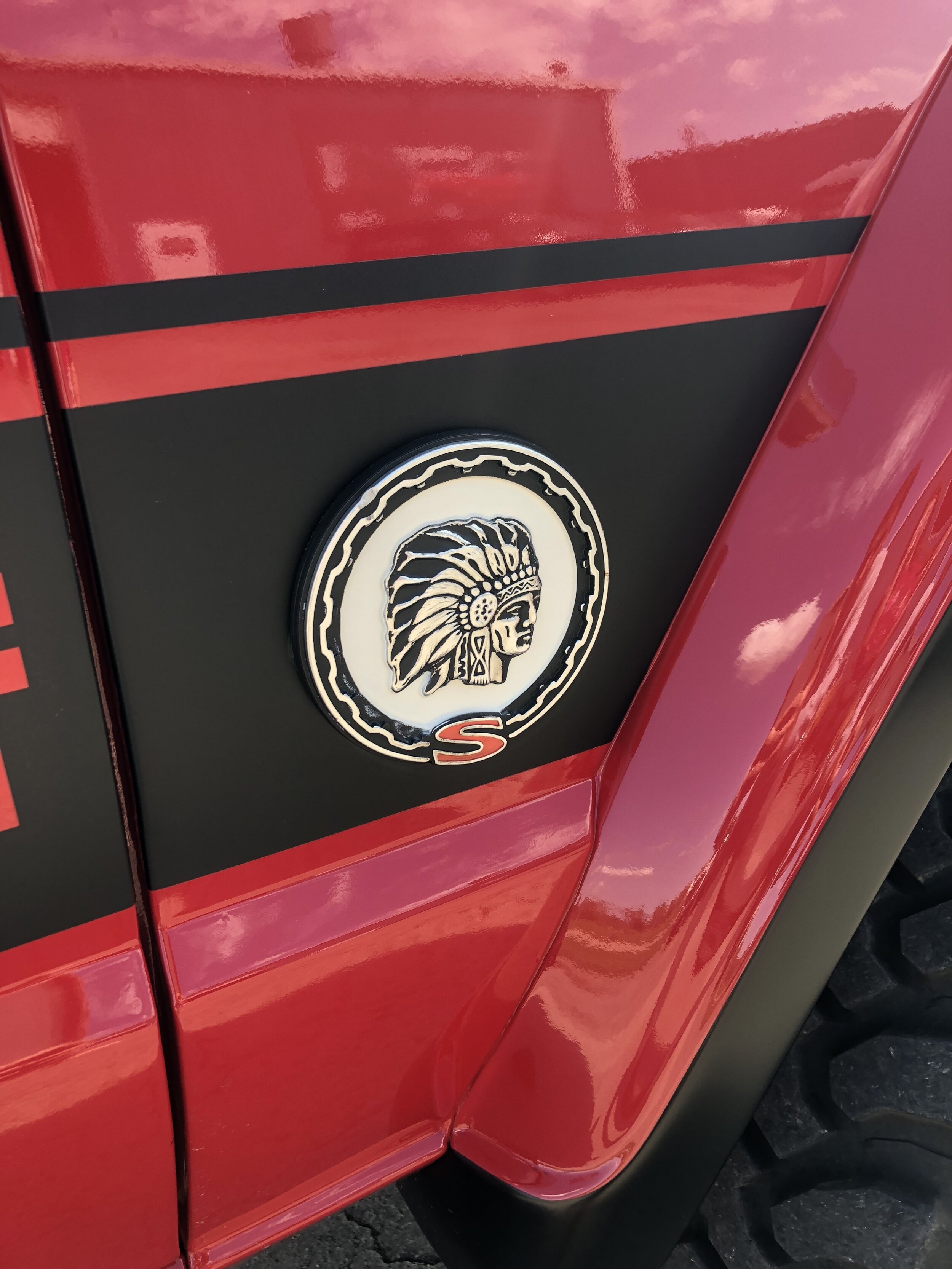
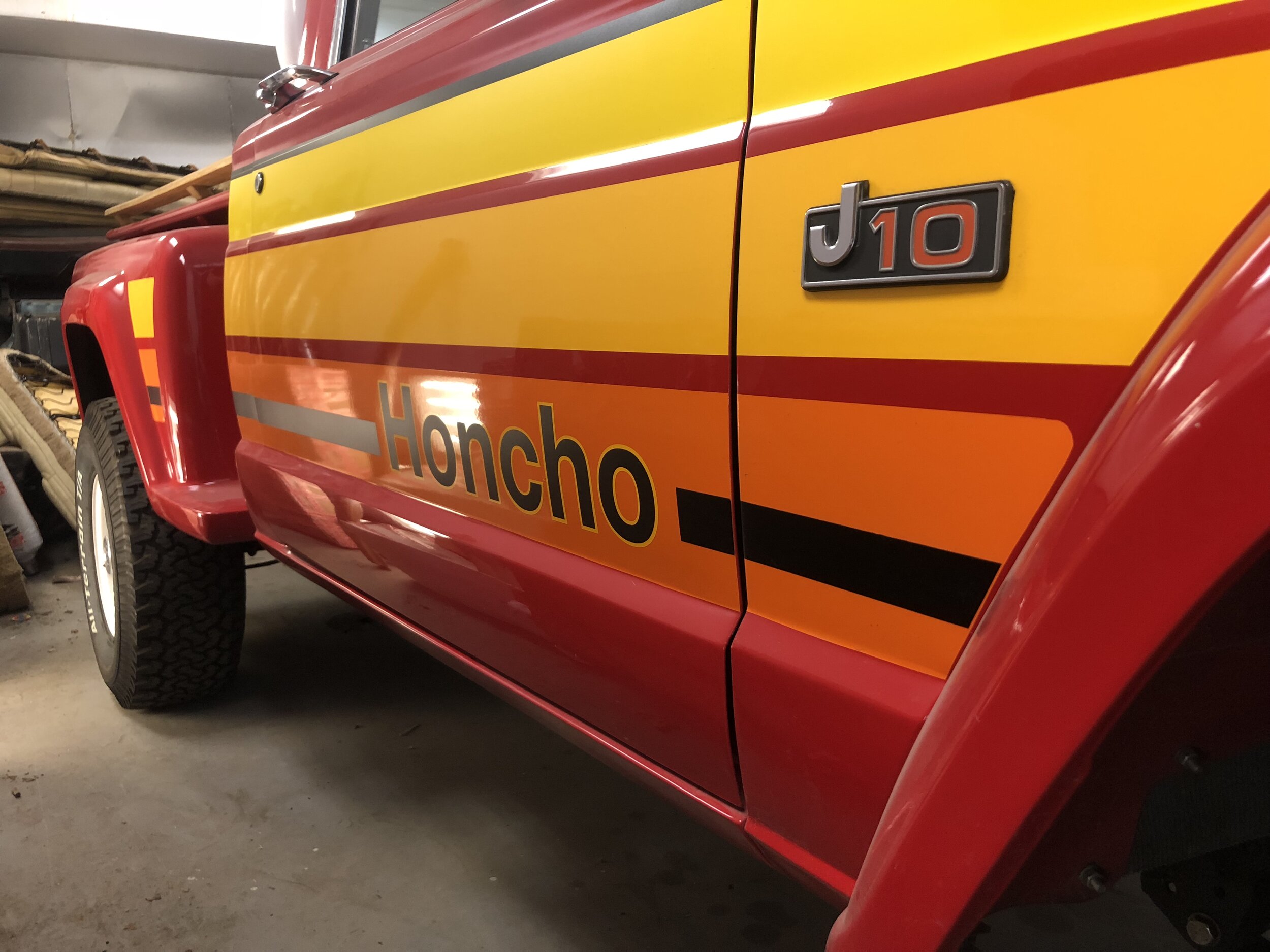
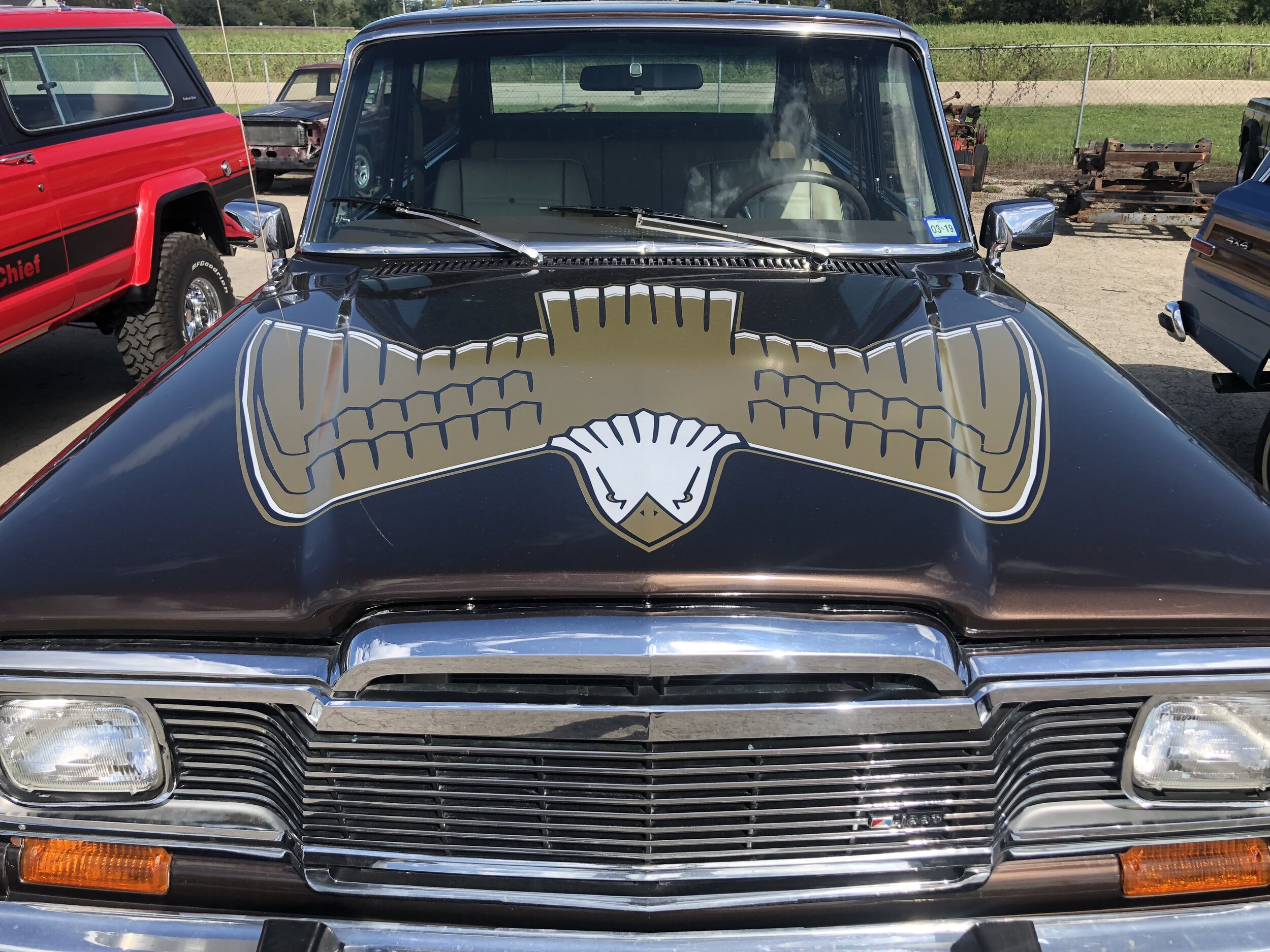
The process first begins by sourcing quality classic vehicles or customers bringing a donor vehicle to Daniel to have completely rebuilt. From there, a rendering specific to each customer is created based on desired design details and customizations. Once the rendering is approved and the Jeep Heritage team has taken delivery of the vehicle for rebuild, the fun begins.
Each vehicle is completely disassembled. Every nut, every bolt, everything. The vehicle is literally stripped down to the bare frame so that each part can be reviewed and determined whether it’s useable for the rebuild or needs to be replaced with new “old” stock – parts that have been purchased from old dealership stock that’s OEM and never used – or with equivalent inventory should a part not be available. From there, the frame, body, and all metallic components are completely blasted, and the hardware and moving parts are cleaned and zinc treated. The frame is then zinc rich primed and then powder-coated and if desired, it can be hot dip galvanized to allow zinc to merge with the metal throughout all its crevasses and cavities, then powder-coated for additional protection. The frame essentially becomes substantially better than it was when it left the original factory.
A myriad of additional intricacies are completed throughout the rebuild process including the mechanical rebuilding of the engine, tranny, axles, driveshafts, steering box, and all the accessories related to the drivability of the vehicle. All chrome pieces are rechromed or replaced, the interior is completely redone using the highest quality materials, the vehicle is completely rewired with options such as air conditioning, heating, electronic door locks, and other creature comforts available if so desired. The fuel tank is either completely cleaned or replaced altogether, the fuel delivery systems are also cleaned or replaced, brake and fuel lines are reproduced using stainless steel, and all remaining parts are recycled or replaced depending on need and budget. The customer also has a variety of options regarding suspension, drivetrain, exhaust, brakes, axles, steering, paint and insulation, wheels and tires, and electronics. The options and customizations are endless, and the quality is truly impeccable.